9 Types of Screws & When to Use Them
Posted on 06/09/22
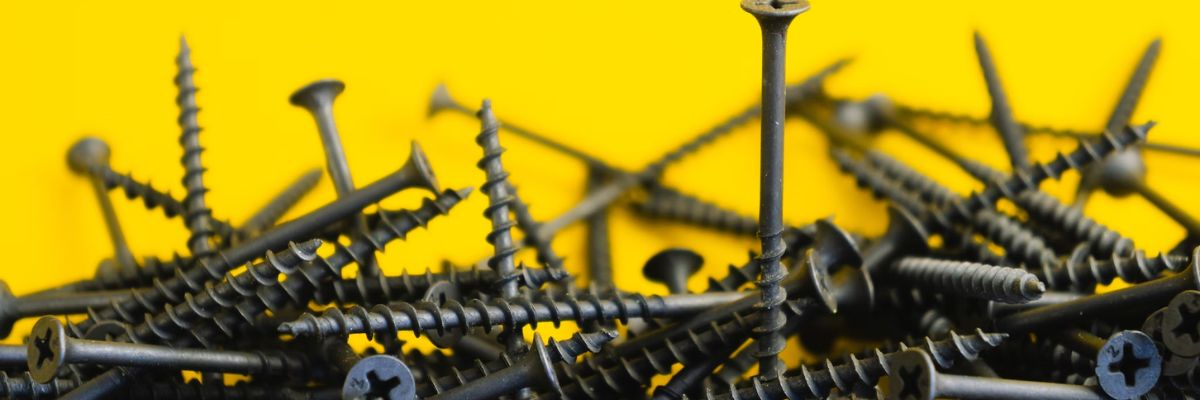
Though they may be small, screws play a mighty role in fastening a vast range of materials together – from use on small-scale projects to buildings and structures.
Though many screws can look fairly similar in appearance, each is designed to fulfil a specific purpose based on their shape, size and thread. Here at ADA, we’ve created a guide to the 9 most common types of screws, as well as advice on when and where to use them.
Why Use Screws?
With so many fixings and fastenings available, it can be overwhelming to decide on the right product to choose. Essentially, screws are used to hold things together – though there are multiple different types that will each be best suited to certain materials and projects.
One of the main advantages of using screws is that they are quick and easy to apply – there isn’t a period of time needed for drying, like when you use glue, for example. Screws can be easily positioned into place and then secured without any additional skills or specialised tools being required.
Parts Of A Screw
Head
The head is the top, rounded part of a screw – the part that will be visible once the screw has been installed. The head of a screw enables it to be turned and driven into materials by different tools such as wrenches or screwdrivers. Different screws are available with different head designs so that various instruments and tools can be used, allowing force to be distributed effectively. In most cases, the head of a screw will be larger than the body of it, so that the screw cannot be driven down deeper than its length.
Shank
The shank of a screw begins directly below the screw’s head. The shank refers to the smooth, cylindrical part of the screw – which is the part that is driven into materials. Screw shanks are manufactured in different sizes, with their diameters indicated by a number. The larger the shank is, the thicker the screw is.
Threads
The threads of a screw are the ridges that wrap around the shank and are used to help secure the screw in place. Both the shank and threads are driven into materials, with threads also available in varying sizes. Screws can be fully threaded, or just threaded in part – meaning the threads stop on the shank, before reaching all the way up to the head.
Tip
The tip of a screw refers to the pointed end, used to help guide the screw into the specific, desired location. The tip may look different depending on the type of screw you’re using; self-drilling screws, for instance, will have a pointed tip with a split in, to enable it to cut into wood. However, machine screws, for example, won’t have a pointed tip at all and will instead be flat at the end.
Types Of Screws
Here are 9 types of screws and when to use them.
Drywall Screws
Pro’s
|
Con’s
|
Designed to countersink without causing damage to dry walls
|
They have a unique dimple on the head of the screw that requires a specific drill bit
|
Self-tapping head design
|
The specific drill bit isn’t commonly available in standard drill sets
|
When To Use Drywall Screws
As the name suggests, drywall screws are used for installing drywall. They’re commonly the standard fastener for securing and attaching drywall sheets to ceiling joists or wall studs. Drylining screws are durable and can provide a strong and lasting hold.
Masonry Screws
Pro’s
|
Con’s
|
Heavy-duty screws used for working with masonry and concrete
|
Holes often need to be pre-drilled before masonry screws can be screwed in
|
When To Use Masonry Screws
Masonry screws, also known as anchors, typically consist of a rounded head and a flat tip – meaning that pre-drilling is required, as there is no point to bore holes. These types of screws are heavy-duty, and can be used for a range of different base materials such as brick, mortar and concrete. Masonry screws are generally manufactured from either carbon steel or stainless steel.
Self-Tapping Screws
Pro’s
|
Con’s
|
No need to pre-drill
|
Can often snap easily if over-tightened
|
Can be used for different materials such as brick, metal and wood
|
Pulling self-tapping screws out leads to stripping the screw
|
When To Use Self-Tapping Screws
Self-tapping screws can tap threads into materials, with no pre-drilling necessary. Self-tapping screws can be ideal for use on areas and surfaces where you are not able to secure the rear end with a nut. These screws can be used on a wide variety of materials, such as plywood, fibreglass, aluminium, brass, polycarbonates and more.
Wood Screws
Pro’s
|
Con’s
|
Ideal for use on woodwork and basic wood construction
|
Different types of threads / heads may cause confusion when looking for right type
|
Available in both interior and exterior styles with different finishes for both
|
The right type of drill bit is required to create an initial pilot hole
|
When To Use Wood Screws
Generally made of brass, bronze or steel, wood screws are designed for attaching wood to wood. Consisting of a smooth shank, coarse threads and a tapered head, wood screws are manufactured to smoothly penetrate through coarse wood fibres without causing additional splintering, due to their minimised resistance.
Hammer-Drive Screws
Pro’s
|
Con’s
|
Designed for heavy-duty use
|
A pre-drilled pilot may be necessary
|
Extremely strong and durable – will stand the test of time
|
You must ensure the screw is a harder material than what it’s being driven into
|
When To Use Hammer-Drive Screws
Also known as U-drive screws, hammer-drive screws are a strong, heavy-duty fastening commonly used for attaching signs and nameplates to walls. Hammer-drive screws can be driven in quickly and easily with tools such as hammers, mallets or other hammer-driven devices.
Deck Screws
Pro’s
|
Con’s
|
Corrosion-resistant
|
Deck screws can often lack strength
|
Many deck screws are self-tapping and are available in a wide variety of lengths depending on their purpose
|
Only ACQ compatible deck screws should be used on certain decking (e.g. pressure-treated wood decking)
|
When To Use Deck Screws
Very similar in their design to wood screws, deck screws are ideal for attaching decking to deck frames or composite decking. Though they aren’t always the strongest option compared to other screw varieties, deck screws are extremely durable – their corrosion-resistance making them ideal for exterior use. The head of a deck screw is specifically designed to countersink, enabling the screw to either sit flush with the wood, or sink slightly into it.
Multi-Purpose Screws
Pro’s
|
Con’s
|
Incredibly versatile – suitable for lots of different projects
|
Often not as durable or strong as specialised screw types
|
When To Use Multi-Purpose Screws
Multi-purpose screws are great for using on a wide range of different DIY projects and developments – ideal for use when working into plastic, chipboard or wood. Often a lower cost alternative to other screw types, multi-purpose screws are available in a variety of threads, lengths and sizes to best suit the material you’re driving them into.
Pocket Screws
Pro’s
|
Con’s
|
Can be ideal screws for using in woodwork and joinery
|
Should be avoided in locations where the screws will be visible
|
When To Use Pocket Screws
Self-drilling, pocket screws are known for their wide head that encompasses the flat shoulder made by drilling pocket holes. Pocket holes aren’t very aesthetically pleasing, and are generally used when they can be hidden, or when using plugs and ultimately painting the wood.
Hex Bolts
Pro’s
|
Con’s
|
A great screw for using when fastening wood to metal
|
May require a drill and wrench for appropriate fastening
|
When To Use Hex Bolts
Hex bolts, known for the hexagonal head and small threads, are ideal for fastening wood to metal. This type of screw is great for using on interior projects, though there are now many varieties available for exterior use too, made from steel.
How To Insert Screws Safely
Here’s how to safely insert screws without power tools or drills
- First, you’ll need to use a hammer and a nail to make a pilot hole – this will make the process a lot easier and safer. Mark the part of the wood or other material that you want inserted, and place the tip of the nail on the mark. Next, gently tap the nail with a hammer – ensure you are wearing any personal protection equipment necessary
- Once the nail has been inserted partially, use a scrap block of wood placed next to the nail to then enable you to sink the nail into the hole – make sure you do this straight. Once inserted deep enough, remove the nail, being careful to do this gently to avoid splitting or splintering the wood.
- Next, insert the tip of your screw into the hole, and using a screwdriver (make sure you’re using the correct type that is compatible with the screw) place it into the slot of the screw’s head. Then you’ll need to slightly push, gently, while turning the screwdriver clockwise.
- Make sure both are aligned correctly and are perfectly straight, and keep going until the screw has tightly sunken into the wood – make sure you avoid cranking the screwdriver, as this can cause damage to the screw itself.
How To Remove Screws Safely
Removing screws is really simple and easy. Here’s how to safely remove screws with a screwdriver.
- First, you need a screwdriver (the same one you used to insert and drive the screw into the material initially).
- Place the screwdriver back into the slot of the screw’s head and gently but firmly turn it anticlockwise.
- Continue doing this until the screw is fully released, or until the threads are fully out of the hole, enabling you to gently pull the rest of the screw out.
- If the screw is stubborn, try using a shorter screwdriver with a larger head – applying downward pressure, repeat the above steps and the screw should come loose.
How Can You Remove A Screw With No Head?
If the screw you are attempting to remove has no head, here is how to remove it safely.
- First, you’ll need a screw extractor – this tool is made from hard steel and is similar in appearance to a standard drill bit. Screw extractors come in a range of different sizes, so be sure to choose a suitable one that will fit the screw you need to remove.
- Next, you need to drill a pilot hole – using a bit with a smaller diameter, you need to bore a hole into the middle of the screw gently; be sure to use safety equipment to do this if necessary.
You should be able to determine how much you need to drill based on both the size of the extractor and the broken screw head itself.
- Next, you need to attach a grip to the extractor – this may be in the form of a locking plier or a T-handle. Then, place the extractor into the pilot hole and use appropriate pressure to tap the extractor into the hole using a hammer.
- Once firmly fitted into the pilot hole, turn the extractor in the same motion you would use to turn in a screw – this will enable the tapered end of the extractor to penetrate the broken screw.
- The extractor should firmly be attached to the shank, and the screw can now be removed. Be sure to sand any rough edges back down with sandpaper for a smooth surface.
How Can You Remove Rusted Screws?
Rusted screws can prove incredibly stubborn, but they can be removed with a little effort. Using a metal hammer, strike the screw two or three times harshly, in order to break the rust seal that is coated around the screw, causing it to be stuck. Then, use a commercial rust penetrant and spray the area – this will soak into the screw and act as a lubricant, helping to loosen the rust. The screw should then be able to be removed.
Frequently Asked Questions
Here are some of the frequently asked questions we receive about screws and their uses.
What Is The Difference Between A Screw and A Bolt?
While even the most experienced woodworkers can dispute this, it is generally agreed that a bolt is referred to as a fastener that goes completely through two materials with a nut attached. A screw, however, pulls two pieces of material together and has only its head visible in the final result.
How Do You Measure A Screw?
In order to measure the diameter of a screw, you need to measure the distance from the outer thread (on one side of the screw) to the outer thread on the other side of it. This measurement is referred to as the major diameter, and will give you an accurate size.
How Many Screws Per Deck Board?
To ensure both stability and durability, it is recommended that each deck board be fastened with two screws at each point in which a board crosses a joist. Boards need to be fastened to rim joists with a total of three screws.
Can You Screw Directly Into Plasterboard?
It is not recommended that you screw directly into plasterboard. The reason for this is, even though the screw may feel firm and tight, fixing it this way doesn’t provide any strength and as soon as weight is put on the screw, it will soon fall straight out.
Can You Screw Into UPVC?
For window frames that are UPVC, experts suggest self-tapping screws be used – this is due to these types of screws being specifically manufactured for caving into the hole they create.
How Are Screws Made?
With so many different types of screws available, it begs the question of how these versatile and useful fixtures are created. The production process begins with wire, which is then uncoiled, straightened and then cut to the precise and desired length. Next comes cold forging, in which the steel is moulded into its specific shape – this is done at room temperature. Then the head of the screw is created, formed by forcing the steel into a variety of dies at a very high pressure. Next, the threads of the screw are formed by rolling or cutting, before the fixture is exposed to extreme heat in order to harden the steel. Surface treatment is the next stage, so this will depend on the screw itself and what the final product is meant to be – for example, zinc-plating may be applied here in order to create a screw that reduces corrosion. Finally, each screw goes through quality control measures to check for uniformity, before being packaged and shipped.
At ADA Fastfix, we have an extensive range of screw and accompanying products to choose between. Take a look at our pages of stock or contact our team if you require further assistance.